
When Is It The Right Time To Select A Manual Chuck Over A Power Chuck?
This statement could easily be reversed since there are benefits for both chuck types. Power Chuck benefits are very clear…consistent gripping power on each part… clamping/unclamping is much faster…chuck’s speed is usually faster and provides less chance of human error.
However, going back to that old saying “everything has a purpose” holds true in many instances for selecting a Manual Chuck over a Power Chuck. Sensitivity to clamping thin walled parts is a major key in using a Manual Chuck, where the clamping pressure can be better adjusted to hold the part without distortion. Also, more jaw adjustment is available in a Manual Chuck.
A perfect example is Atlas Precision Machining in South Windsor, CT, a manufacturer of thin-walled aerospace stators which are made of various exotic aerospace materials.
Since being founded in 1999 by owner, Walter Dybinski, Atlas has continued to increase their CNC turning capabilities from 1” to 28” diameters. Because these thin walled larger parts are more apt to distort easily (as well as being much more difficult to access) it became necessary to invest in larger CNC VTL’s with improved chucking methods,
Until recently, Atlas’ approach was to use independent Manual Chucks with step jaws or pinch jaws. Although this process was successful, it proved to be very time consuming for the set-up and increased the margin of error for the operator. In addition, had they selected Hydraulic Chucking, the clamping sensitivity to these parts would be lost, leading to inconsistent or scrap parts.
In 2011, Atlas purchased (2) Okuma CNC V100 VTL’s from The Robert E. Morris Company, Windsor, CT, to increase their turning capacity up to 45 inches. Investigating the options for clamping, Robert E. Morris Company then contacted Royal Machine & Tool to discuss the new requirements and requested that Royal Machine’s Engineering Department review the two newly acquired Okuma V100 VTL’s on site. In turn, two 32” Diameter 3-Jaw wedge operated Manual Chucks were recommended to provide a finer feel for the operator when clamping the stators.
Jeff Dybinski, Atlas General Manager, stated, ”Having developed a close working relationship with Royal Machine, we relied on their recommendation of using the wedge chuck design over the more common scroll type chuck for a number of reasons. The wedge chuck is operated by a commercially available bevel gear assembly, providing more consistent and evenly distributed clamping and sensitivity to the clamping of the part. Also, with the actuation via the wedge, there is a better distribution of the clamping, providing better sensitivity to the clamping of the stators. The Top Tooling applied is Pie Jaws bored and faced in place on the machine, providing grip on the complete diameter.”
“After six months of continuous production, we have seen our production increase along with the quality our customers require. Set up and changeover are improved and now it is only a matter of time before we may decide to increase our capacity beyond the 45” diameter.”
Royal Machine & Tool designs and builds chucks in sizes up to 72” in diameter…either power operated or manually operated. All chucks are built and tested in the USA.
Founded in 1956, Royal Machine & Tool Corporation is ISO9001:2008 & AS9100 Rev. “B” Certified and serves the world’s leading industries from its Berlin, CT corporate offices and manufacturing facility representing over 40,000 square feet including state-of-the-art CNC machine tools. All services and products are performed/produced in the USA and include the designing and building of custom and standard work holding devices from simple manual fixtures to sophisticated hydraulic fixtures with multiple faces. Custom and standard chucks of all types for rotating and non-rotating applications are also designed and built by Royal Machine &Tool…as well as a complete range of Contract Machining options/services from single prototype machining to high volume production requirements.
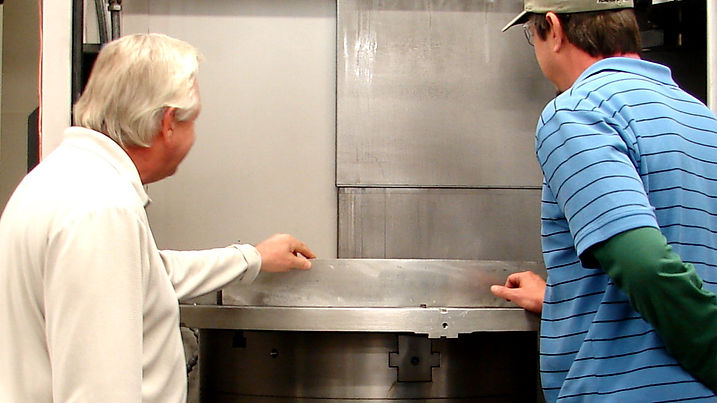
Atlas Precision Machining owner, Walter Dybinski (left) and General Manager, Jeff Dybinski, discuss and review the set-up for the next style of Stator

Typical stator after having been machined on the Okuma VL 100 and Royal Machine Manual Chuck